This comprehensive guide breaks down the entire customization process—from material selection to factory workflows. Whether you’re launching a new product line or refining your sourcing strategy, this article will equip you with critical manufacturing knowledge.
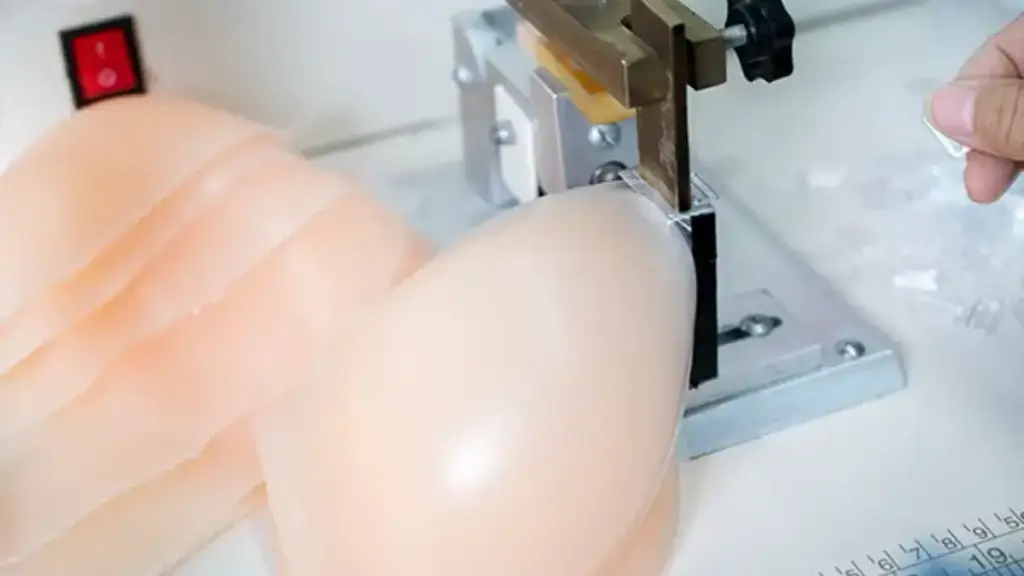
Overview of Silicone Bra Types and Customization Possibilities
Before diving into how to customize silicone bra in a factory, it is important to understand the product categories available for customization.
The table below summarizes the most common types of silicone bras manufactured at scale:
Type | Caratteristiche principali | Advantages | Target Users |
Classic Adhesive Bra | Two adhesive cups, no straps | Invisible under clothing, riutilizzabile | General users, fashion wear |
Front Closure Push-Up | Clasp between cups, strong cleavage lift | Enhanced cleavage, secure fit | Young consumers, party wear |
Winged Adhesive Bra | Extended side flaps for added support | Better adhesion and coverage | Larger bust sizes |
Lift-Up Bra | Adhesive tabs for vertical lift | Natural lift, minimalist design | Petite users, formal wear |
Copricapezzoli in silicone | Lightweight, round covers | Ultra-discreet, easy to use | Minimalist users, daily wear |
Each type offers varying levels of support, aesthetics, and customization potential, such as adhesive grade, color matching, logo imprint, and packaging options.
Key Materials Used in Silicone Bra Manufacturing
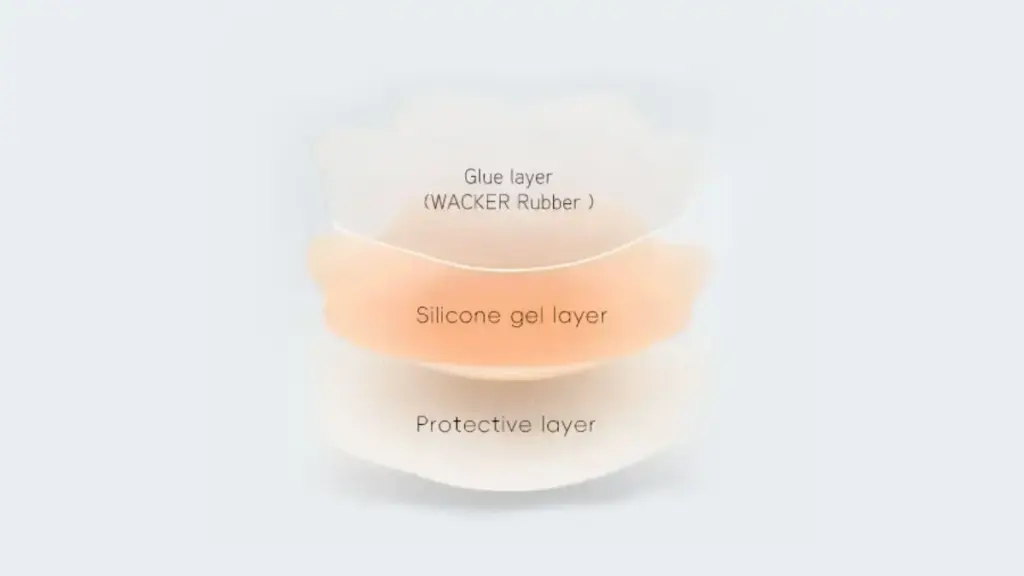
Material selection significantly impacts the quality, comfort, and durability of silicone bras. This is especially important for products designed for prolonged skin contact.
- Silicone Gel: The main filling material, available in varying densities. Platinum-cured types meet FDA and LFGB standards for skin safety.
- TPU Film (Thermoplastic Polyurethane): Used as the external layer to contain the gel, known for flexibility and durability.
- Medical-grade adhesives: Ensure secure adhesion to the skin without irritation. Types vary based on use-case: single-use vs reusable.
- PET Protective Films: Applied post-production to protect adhesive surfaces before consumer use.
For those investigating how to customize silicone bra in a factory, selecting the right material configuration aligned with end-user expectations and market regulations is a critical first step.
Step-by-Step Process to Customize Silicone Bra in a Factory
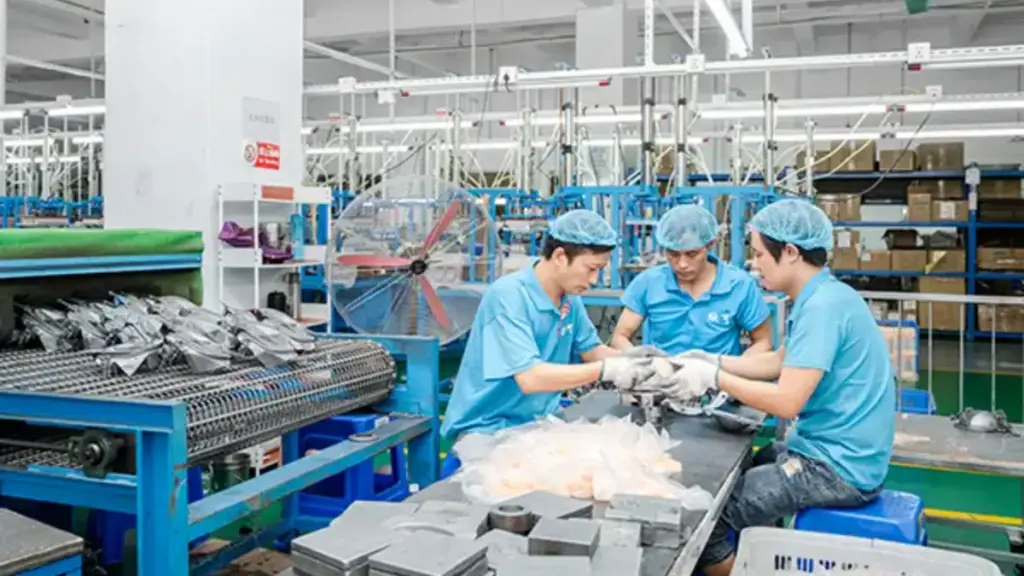
At XKSilicone, the silicone bra manufacturing process follows a precise and quality-controlled workflow, combining material expertise, engineering precision, and decades of industry experience. Below is an in-depth breakdown of each step involved in customizing silicone bras.
Raw Material Preparation
The process begins with selecting high-grade platinum-cured silicone gel, known for its skin safety, durabilità, and compliance with international certifications such as REACH, E SGS. To ensure a natural appearance and feel, the gel is adjusted for specific softness (Shore A hardness) and color-matched using pigment blending. Accurate skin-tone simulation is critical, especially for clients requiring customized color options across global markets.
Injection Molding (Gel Filling)
Silicone gel is injected into pre-heated molds that define the shape and volume of each bra cup. Mold designs are tailored based on client specifications—ranging from A to E cups—and allow for thickness variations from 8 mm to 20 mm depending on lift or coverage requirements. Mold temperature and pressure are closely regulated to maintain uniform density and prevent bubble formation.
Fabric and PU Film Lamination
Once molded, each cup is covered with a medical-grade polyurethane (PU) film, often combined with soft-touch fabric. The film acts as a skin-safe barrier and also supports adhesion of the gel to the outer surface. Lamination is done using precise alignment tools to avoid wrinkles or stretching.
Adhesive Coating
On the inner surface, a pressure-sensitive adhesive is applied in clean-room environments to maintain purity and hypoallergenicity. The coating must be uniform to ensure consistent adhesion across various skin types and humidity conditions. XKSilicone uses a proprietary adhesive formula optimized for sweat resistance and reusability.
Edge Sealing and Surface Polishing
Edges are sealed using thermal bonding techniques to create smooth, non-irritating contours. Each unit undergoes surface polishing to enhance transparency and eliminate visual imperfections. These steps are essential for ensuring wearer comfort and aesthetic appeal.
Curing and Final Shaping
The bra cups are placed in a temperature-controlled oven (typically 80–120°C) for thermal curing. This stabilizes the adhesive and finalizes the structural form. Additional trimming may be performed to ensure symmetry between pairs.
Inspection and Packaging
Each batch is subjected to dimensional checks, visual inspection, and adhesion strength tests. XKSilicone, adheres to a 5S production methodology—Sort, Metti in ordine, Splendore, Standardizzare, Sustain—ensuring that every silicone bra meets strict quality control benchmarks. Products are then packaged based on client branding or private label requirements.
This structured and traceable production process ensures consistent results, reinforcing commitment to reliability and cosmetic-grade manufacturing.
OEM vs ODM and Customization Options
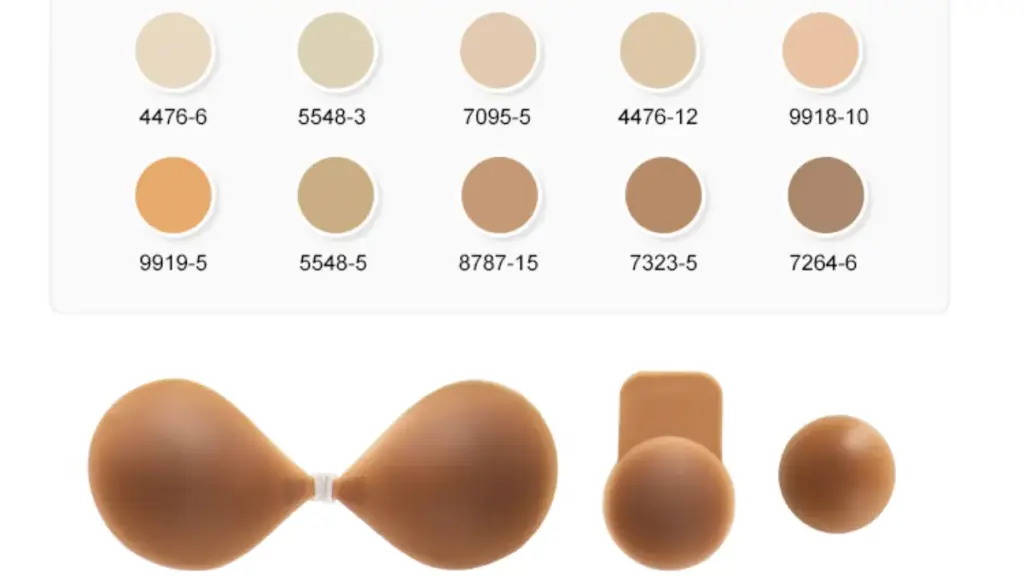
In silicone bra manufacturing, understanding the difference between OEM (Produttore di apparecchiature originali) e ODM (Produttore di design originale) helps brands choose the right customization path. OEM allows clients to provide specific design requirements and brand assets, ideal for private label brands. ODM offers semi-finished models for light customization, reducing development lead time and cost.
Personalizzazione options are critical to meeting diverse market needs. Here are the key areas:
- Cup Thickness: Options typically range from 8mm to 20mm. Thicker cups (15–20mm) offer stronger push-up effects and are suited for formal or evening wear, while thinner options (8–12mm) are preferred for natural shaping and comfort in daily wear.
- Shape and Contour: Most factories offer round, lacrima, and winged shapes, along with either a flat or curved inner contour. Winged styles add support for fuller busts, while teardrop shapes suit smaller frames seeking lift.
- Tipo adesivo: Options include medical-grade silicone gel and pressure-sensitive acrylic, tailored to skin type, riusabilità, and regional climate.
- Corrispondenza del colore: Factories often provide 4–6 standard nude tones. For precise skin tone match, Pantone code referencing or on-skin sampling is used.
- Logo and Branding: Clients can add embossed logos, printed labels, or even QR codes for authenticity.
- Confezione: Custom boxes with insert trays, magnetic closures, or eco-packaging are available to align with retail goals.
These options ensure your brand can align product performance with market expectations while keeping production scalable and consistent.
Quality Control Standards in Silicone Bra Manufacturing
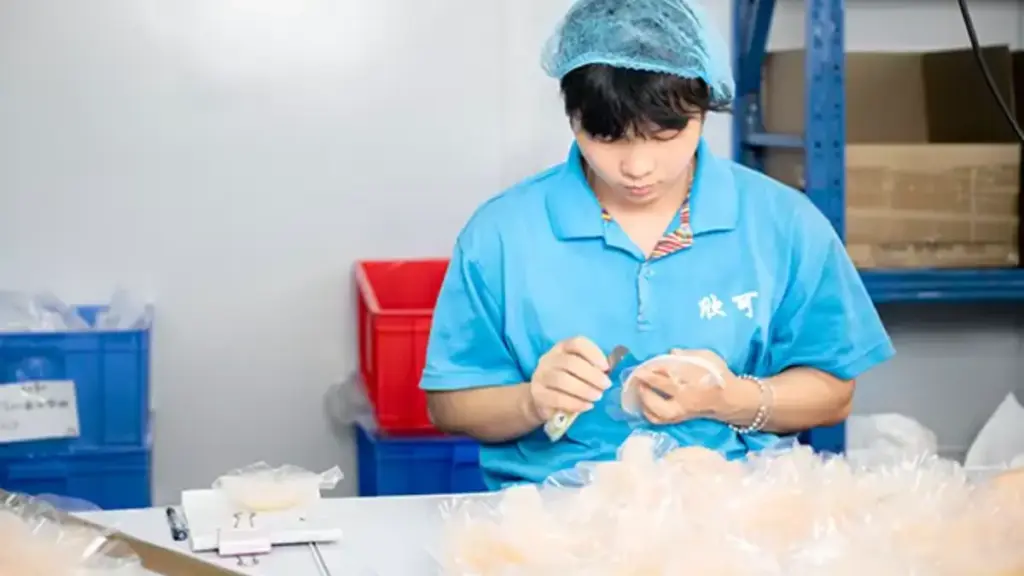
Strict testing helps address common concerns like “Il reggiseno al silicone è buono per la salute?” by ensuring hypoallergenic, certified skin-safe materials. Factories aiming to deliver consistent, sicuro, and high-performance products typically establish multi-layered QC systems aligned with international quality standards.
- Incoming Material Inspection
Silicone viscosity, gel clarity, and adhesive quality are tested.
Material certification review (FDA, REACH).
- In-Process Inspection
Mold temperature, curing time, injection pressure monitored.
Random sampling for visual symmetry, air bubble check.
- Final Product Inspection
Adhesion Test: Peel strength under load.
Durability Test: Reuse cycles under heat and humidity.
Dimensional Check: Consistency in shape and thickness.
Skin Sensitivity Test (optional): Using hypoallergenic evaluation.
- Batch Documentation
Retention samples, production logs, and test reports are archived for traceability.
Most high-standard facilities operate under ISO 9001 or ISO 13485 for medical-related silicone items. Adopting these systems not only ensures safety but also builds client trust and long-term cooperation—especially vital when exploring how to customize silicone bra in a factory with international clients in mind.
How to Choose the Right Silicone Bra Manufacturer
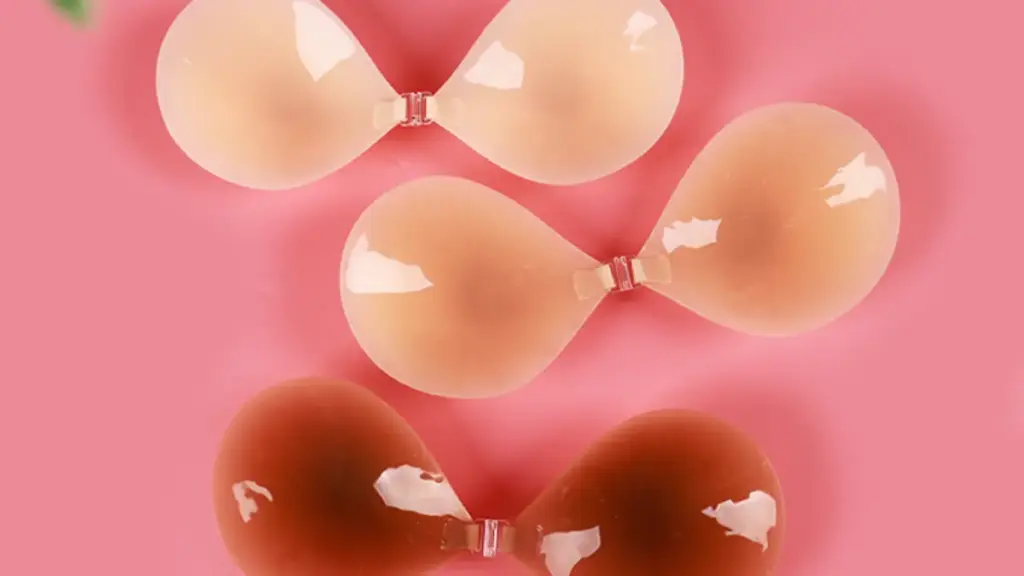
Selecting a reliable silicone bra manufacturer requires a multi-angle evaluation that goes beyond cost. Below are two key dimensions to guide your decision:
Lead Time, Moq, and Cost Considerations
Production efficiency, minimum order quantity (Moq), and pricing transparency are fundamental. A capable factory should commit to lead times of 15–30 days depending on customization complexity, while offering scalable MOQs starting at 1,000 coppie. Clear cost structures with tooling, sampling, and packaging fees outlined upfront help avoid unexpected charges.
Technical Capacity and Compliance Standards
Assess the factory’s engineering and quality control capabilities. Key factors include in-house mold development, ability to customize adhesive strength based on skin type, and experience in international compliance. Factories holding certifications such as SGS and REACH are better equipped to serve regulated markets and ensure product safety.
Recommended Silicone Bra Manufacturer
GZXKSilicone, a specialized silicone bra supplier, stands out for its strict application of the 5S methodology (Sort, Metti in ordine, Splendore, Standardizzare, Sustain) throughout production. Their products are certified with MSDS, SGS, CA65, e RAGGIUNGERE, meeting high international safety standards. With deep OEM/ODM experience, precision molding, and color matching expertise, XKSilicone is a trusted partner for global private labels seeking scalable, compliant solutions.
Mastering the process of how to customize silicone bra in a factory requires a deep understanding of material science, adhesive performance, mold precision, and regulatory compliance. This guide has walked you through the key steps, Opzioni di personalizzazione, manufacturing models, and supplier evaluation criteria to support informed sourcing decisions.
For brands seeking reliable, scalable, and fully customizable silicone bra solutions, partnering with XKSilicone is a strategic move to ensure both product integrity and market success.